عوامل خرابی بیرنیگ ها
مقدمه علت های اصلی در خرابی بیرینگها: مهم نیست که چه کاری انجام می دهید؛ همیشه این احتمال وجود دارد که محصولات از بین بروند. همین امر در مورد بلبرینگ نیز صادق است اما این نکته بدان معنی نیست که شما نمی توانید از بسیاری از مواردی که منجر به خرابی پر هزینه می شود جلوگیری کنید.
این مقاله راهنمایی برای بررسی علل اصلی خرابی بیرینگها و همچنین نحوه جلوگیری از وقوع آنها است. با کسب اطلاعات بیشتر در مورد این مشکلات احتمالی و دانستن نحوه متوقف کردن آنها، می توانید بیشترین عمر ممکن را از بلبرینگ خود توقع داشته باشید.
روانکاری نامناسب
طبق یک مطالعه جدید، تا ۸۰ درصد از خرابی بیرینگها ناشی از روانکاری نادرست است. این امر شامل روانکاری ناکافی، استفاده از روان کننده های نامناسب و یا دمای بیش از حد است که باعث کاهش عملکرد روانکار می شود.
از نوع مناسب و مقدار کافی روان کننده استفاده کنید. از ریزش گریس خودداری کنید، فواصل مناسب برای روانکاری را دنبال کنید و از قوانین روانکاری بیرینگها پیروی کنید.
آلودگی
آلودگی معمولا ناشی از ورود مواد خارجی به روان کننده ها یا محلول های تمیزکننده است. از جمله این موارد که منجر به خرابی بیرینگها می شود می توان به ورود خاک، گرد و غبار و تراشه های فولادی ناشی از محل های آلوده و دست یا ابزار کثیف اشاره کرد.
روان کننده را فیلتر کنید و ابزار را تمیز نگه دارید تا خطر آلودگی کاهش یابد.
نصب نادرست
در بیشتر موارد، یاتاقان ها باید با فشار روی حلقه چرخان سوار شوند.
دستورالعمل های مناسب نصب را دنبال کنید و اطمینان حاصل کنید که همه کارکنان تفاوت بین نصب صحیح و نادرست را درک می کنند.
تنظیم نادرست
شفت های خم شده، شانه های خارج از مربع شفت، فاصله های خارج از مربع و نصب نادرست به دلیل شل بودن اتصالات می تواند منجر به گرمای بیش از حد و خرابی جداکننده شود.
شفت ها و محفظه ها را برای عبور از شانه ها بررسی کنید و از آویزهای درجه یک استفاده کنید.
برینلینگ کاذب
حرکت سریع ساچمه ها در یک مسیر آزاد در حالی که تجهیزات به دور از روانکاری هستند و عدم چرخش یاتاقان که اجازه نمی دهد تا روان کننده تازه به محل برگردد، منجر به ایجاد برینلینگ کاذب و خرابی بیرینگها می شود.
لرزش های خارجی که می تواند باعث حرکت ساچمه ها شود را از بین ببرید. همچنین، حتما از روان کننده های حاوی مواد افزودنی ضد سایش استفاده کنید.
خوردگی
رطوبت، اسید، گریس با کیفیت پایین، بسته بندی ضعیف و تراکم ناشی از دمای بیش از حد، می تواند باعث خوردگی شود.
مایعات خورنده را از اطراف بلبرینگ دور کنید. استفاده از مواد مناسب بلبرینگ مانند فولاد ضد زنگ می تواند به شما کمک کند تا از ایجاد یک محیط خورنده جلوگیری کنید.
آسیب الکتریکی
عبور مداوم جریان متناوب یا مستقیم، حتی با جریان کم، می تواند به آسیب الکتریکی منجر شود.
با استفاده از یاتاقان های عایق بندی شده، از ورود جریان های الکتریکی به داخل یاتاقان جلوگیری کنید.
خستگی
ورقه ورقه شدن اغلب نتیجه فشار بیش از حد، حلقه داخلی تنگ و استفاده از بلبرینگ بیشتر از عمر محاسبه شده آن است.
بیینگ را جایگزین کنید و یا یک طراحی مجدد را در نظر بگیرید که از یک بلبرینگ با طول عمر خستگی بیشتر و توصیه های مناسب برای شفت استفاده می کند.
گرمای بیش از حد
گرمای بیش از حد به طور کلی نتیجه دمای بیش از حد کار و روانکاری نادرست است. درجه حرارت بالا باعث پاک شدن گریس و کاهش راندمان روغن می شود. در شرایط درجه حرارت بالا، اکسیداسیون می تواند منجر به از بین رفتن روغن های روان کننده از گریس شود و یک صابون خشک و پوسته پوسته باقی می ماند. درجه حرارت بالاتر همچنین سختی فلز را کاهش می دهد و باعث نارسایی اولیه می شود.
کنترل های حرارتی یا اضافه بار، مسیرهای حرارتی کافی و خنک کننده های اضافی از بهترین گزینه ها برای کاهش گرمای بیش از حد هستند.
بار بیش از حد
قرار دادن بار بیش از حد بر روی یاتاقان نیز یکی دیگر از دلایل اصلی خرابی بیرینگها است.
بار را کاهش دهید یا با استفاده از یاتاقان با ظرفیت بیشتر، طراحی مجدد را در نظر بگیرید.
ذخیره سازی و رسیدگی نادرست
ذخیره سازی نادرست در انبار، یاتاقان ها را در برابر رطوبت و گرد و غبار قرار می دهد. نگهداری یاتاقان در دمای بیش از حد نیز می تواند ماندگاری گریس را کاهش دهد؛ بنابراین برای دریافت راهنمای ذخیره سازی همیشه با سازنده گریس در تماس باشید.
یاتاقان ها را در یک منطقه خشک و در دمای اتاق نگهداری کنید. همیشه یاتاقان ها را بپوشانید تا تمیز نگه داشته شده و قبل از باز کردن آنها را به محل نصب ببرید.
منبع مطالب و تصاویر: سایت بتکا
مقاله دوم: علل خرابی بیرینگ ها
زمانی که بلبرینگ ها دچار شکست می گردد ،هزینه سنگینی به ماشین تحمیل می گردد در اولین قدم انتخاب صحیح بلبرینگ برای هر کاربردی ، قابلیت اطمینان به عملکرد صحیح آنرا تضمین می نماید. (کارایی را بالا می برد ) پارامتر هایی مثل بار،سرعت،حرارت ،دقت اجرایی ،زمانی در حد مطلوب ما خواهند بود که، انتخاب صحیح بلبرینگ صورت پذیرفته شده باشد، در محاسبه ی عمر قابل انتظار برای هر بلبرینگ،۴ فرضیه در نظر گرفته می شود:
- روانکاری و روغن کاری به مقدار مناسب در بلبرینگ صورت پذیرد.
- مونتاز بلبرینگ صحیح صورت پذیرفته باشد.
- ابعاد قطعات مرتبط به بلبرینگ صحیح ودرست باشند(مثل اندازه سوراخ نشیمنگاه – عرض- پهنا و …).
- بلبرینگ هیچگونه نقضی نداشته باشد (از نظر تولید و ساخت).
توصیه های تعمیرات و نگهداری به شرح ذیل می باشد.
اگر کلیه موارد بالا رعایت شده باشد، دلیل شکست بلبرینگ می تواند از خستگی مواد اولیه باشد.
خستگی، نتیجه کاربرد تنش های متناوب در قطعات است. به گونه ای که تحمل اینگونه بارها آثاری در سطح قطعه ایجاد می نماید که در عکس های ۱ تا ۳ نشان داده شده است.

خرابی بلبرینگ ها
آغاز شروع خستگی (خستگی پوسته شدن) بر روی سطح اتفاق می افتد. اولین نشانه به صورت خراش های سطحی میکروسکوپی است که قابل دیدن نیستند و همچنین این تاثیرات قابل شنیدن نمی باشد، تا زمانی که ماشین در حین کار است. ( شکل۱)
در شکل ۲ ترک های سطحی ایجاد شده است، که در این وضعیت قابلیت شنیده شدن را دارد. اگر در محیط اطرافتان سطح صدا زیاد باشد ارزیابی وضعیت بلبرینگ توسط یک دستگاه ارتعاش سنج که قادر است به طور معمول پوسته پوسته شدن که در شکل ۲ نشان داده شده اند را تشخیص می دهد.
مدت زمانی که شروع پوسته شدن از (شکل۱) تا حالت پیشرفته (شکل۲) طول می کشد متغیر است و به بار و سرعت بستگی دارد و این امر یک پدیده ی ناگهانی نیست و خرابی بلبرینگ و شکست آن در یک مدت زمان ایجاد می گردد.
شکست کامل بلبرینگ و نتایج خرابی قسمت های مختلف ماشین اغلب اجتناب ناپذیرند ، عملکرد نا منظم دستگاه دلیل سروصدا و ارتعاشات در شافت ها و بلبرینگ های گیربکس است . متأسفانه به ندرت ۴ شرط ارائه شده درعمر و طراحی بلبرینگ رعایت می گردد.
یک اشتباه مشترک و رایج در این زمینه این است که بلبرینگ درحد کافی ظرفیت و تحمل بار را ندارد و باعث شکست بلبرینگ می گردد. همچنین برخی فکر می کنند هر چه قیمت بلبرینگ بیشتر باشد توانایی انتقال بار بیشتر دارد.
یکی از سخت ترین کارها ، آنالیز شکست اولیه بلبرینگ می باشد و به دو بخش تقسیم می شود
علل خرابی بلبرینگ ها قبل از راه اندازی
- اندازه ها و تلرانس های روی شافت اشتباه باشد
- نشیمنگاه بلبرینگ معیوب باشد.(ازنظر تلرانس و نا هم محوری)
- نا هم محوری در حالت استاتیک.
- خطا در مونتاژ.
- عبور جریان برق از بلبرینگ.
- حمل ونقل و انبار داری غلط.
علل خرابی بلبرینگ ها پس از راه اندازی
- روغن کاری نا متناسب و بی اثر(کاهش سطح روغن، انتخاب نوع روغن نامناسب، اشکال در سیستم روغن کاری اجباری)
- سیل های غلط (خرابی کاسه نمدها و مونتاژ اشتباه).
- ارتعاشات در حالت استاتیکی.
- نا هم محوری در حین عمل.
- عبورجریان الکتریسیته بعد از استارت و شروع به کار.
یک روش طبقه بندی شده توسط ISO ( سازمان استاندارد بین المللی ) جهت پدیده ی شکست بلبرینگ ها بر مبنای استاندارد(ISO15243-2004E) است. این استاندارد ،شش نوع شکست را شناسایی و معرفی نموده است که با استفاده از تجهیزات و دستگاه های ارتعاش سنج قابل تشخیص می باشند. بنابراین با استفاده از پایش ارتعاشات قادر خواهیم بود که بلبرینگ ها را قبل از فاجعه به موقع تعویض نماییم ودرهزینه ها صرفه جویی کنیم
منبع تصاویر و مطالب: وبسایت کابرو
مقاله سوم: نشانه های خرابی بیرینگ ها
این یک واقعیت است که بیرینگ ها به طور ناگهانی نمی شکنند. یک رویکرد ناظر و دقیق برای شناسایی علائم هشدار دهنده یک خرابی قریب الوقوع ، می تواند از خرابی ماشین آلات و خسارت های متعاقب جلوگیری کند. روغن های ضد گرد و غبار بر روی بیرینگ ها تا حدودی در مقابل خوردگی از آن ها محافظت می کنند. با این حال ، رطوبت نسبتا بالا و یا حتی تغییرات درجه حرارت قابل توجه در شب ، می تواند بیرینگ را در معرض رطوبت قرار دهد. استفاده معمولی از بیرینگ ها با موارد زیر همراه خواهد بود :
- لرزش جزیی
- سر و صدا در حین کار
- افزایش درجه حرارت در حین کار ( به مقدار کم )
- مصرف برق
- زوال روغن کاری به مرور زمان
افزایش ناگهانی سطح هر یک از این پارامترها نشانه قطعی از خرابی یا توقیف قریب الوقوع بیرینگ است. نادیده گرفتن هر یک از این خرابی ها می تواند منجر به مشکلات جدی شود. این موضوع حتی می تواند باعث خرابی تجهیزات اصلی شود و یا حتی منجر به آتش سوزی گردد. علت خرابی ها در سه دسته طبقه بندی می شود :
- خرابی ناشی از عوامل محیطی
سهل انگاری در نصب ، شرایط کاری کثیف ، روانکاری نامناسب ، بارگیری بیش از حد ، لرزش ، سرعت بیش از حد ، گرمای بیش از حد ، آلودگی
- خرابی ناشی از استفاده نادرست
انتخاب نادرست نوع بیرینگ و یا نصب نادرست
- خرابی ناشی از کیفیت بیرینگ
کیفیت پایین اجزای تشکیل دهنده ، ساختار یا ترکیبی فولادی ، خرابی ناشی از طراحی و تولید قسمت های داخلی ، قفسه و یا کیفیت آب بند
در ادامه عوامل محیطی که ۹۰% منجر به خرابی بیرینگ می گردند را برایتان مشخص کرده ایم! خرابی ناشی از عدم استفاده صحیح و کیفیت پایین به ندرت رخ می دهد. علاوه بر این ، بررسی و تجزیه و تحلیل آنها به ابزار دقیق تحقیق و کنترل کیفیت نیاز دارد.
- خرابی ناشی از عوامل محیطی
سهل انگاری در نصب ، شرایط کاری کثیف ، روانکاری نامناسب ، بارگیری بیش از حد ، لرزش ، سرعت بیش از حد ، گرمای بیش از حد ، آلودگی
- خرابی ناشی از استفاده نادرست
انتخاب نادرست نوع بیرینگ و یا نصب نادرست
- خرابی ناشی از کیفیت بیرینگ
کیفیت پایین اجزای تشکیل دهنده ، ساختار یا ترکیبی فولادی ، خرابی ناشی از طراحی و تولید قسمت های داخلی ، قفسه و یا کیفیت آب بند
در ادامه عوامل محیطی که ۹۰% منجر به خرابی بیرینگ می گردند را برایتان مشخص کرده ایم! خرابی ناشی از عدم استفاده صحیح و کیفیت پایین به ندرت رخ می دهد. علاوه بر این ، بررسی و تجزیه و تحلیل آنها به ابزار دقیق تحقیق و کنترل کیفیت نیاز دارد.
علل محیطی و منشا خرابی بیرینگ ها
خرابی بیرینگ ها به دلیل عوامل خارجی زیادی ممکن است رخ دهد که به طور کلی این علل را به چهار دسته می توان تقسیم کرد :
شرایط نصب
- ابزارها و روش های نامناسب نصب
- شرایط نصب کثیف
- بارهای شوک دهنده در حین نصب
- تولید نادرست قطعات
- احاطه بیرینگ ها با شفت و نشیمنگاه نامناسب ، عدم هم راستایی و غیره
شرایط عملیاتی
- بارگذاری بیش از حد
- ارتعاشات زیاد
- سرعت بیش از حد
- انحراف شفت
شرایط محیطی
- دمای محیط بیش از حد بالا یا بیش از حد پایین
- قوس الکتریکی
- آلودگی ناشی از آب ، خاک ، مواد شیمیایی ، تکه های پارچه و غیره
شرایط روانکاری
- روانکاری نادرست
- عرضه نامناسب روان کننده
- بازه زمانی طولانی روانکاری مجدد
تشخیص عللت خرابی بیرینگ ها
دغدغه اصلی کاربران بیرینگ ها ، تشخیص اولیه علت خرابی بیرینگ قبل از از بین رفتن قطعات است. مراقبت های پیشگیرانه در اصل بهترین راه حل است ، اما در موارد خاص مقدار زمان صرف شده و هزینه های زیاد جهت دسترسی به بیرینگ ها می تواند عامل بازدارنده باشد. برای برخی کاربردها ( همچون صنعت هواپیما ، تهویه هوا و غیره ) مراقبت های پیشگیرانه یک ” ضرورت ” محسوب می شود.
اگرچه ارزیابی میزان فرسودگی بیرینگ ها از طریق نشانه های خارجی کار دشواری است ، اما به عنوان یک قاعده کلی کاربران پس از تشخیص علائم بیرونی باید بتوانند عمر مفید یک بیرینگ را در نظر بگیرند.
نشانه های خارجی علت خرابی بیرینگ ها
چرخش بیرینگ در شرایط عملیاتی ( در حال کار ) پارامترهای معمولی همچون دمای کار ، صدا و لرزش را به همراه دارد. سطح دقیق آن ها به عوامل مختلفی همچون بار ، سرعت ، روانکاری ، نوع بیرینگ و غیره بستگی دارد. بالا بودن غیر طبیعی ” پارامترهای نرمال ” یک هشدار برای خرابی احتمالی در نظر گرفته می شود.
انحراف از ” هنجارهای عملیاتی ” که در ” شرایط عملیاتی ” برای هر یک از موارد زیر ایجاد می شود ، نیاز به مراقبت های پیشگیرانه و یا حداقل یک بررسی نزدیک برای تشخیص علل خرابی دارد.
- لرزش = این مورد را می توان با استفاده از دست و یا تجهیزات الکترونیکی ( آنالیزگر فرکانس و نوسان ) تشخیص داد. هشدار اپراتور بدین معناست که باید دستگاه را متوقف کنید.
- صدا = برخی صداهای غیر طبیعی را ممکن است بلافاصله متوجه شوید ، همچون صدای فرورفتگی اجزای غلتک ناشی از نصب نامناسب. صدا نشان دهنده خرابی اولیه است و تفاوت در شدت و تناوب صدا نشان دهنده میزان خسارت است. خسارت ناشی از بارهای نامتعادل عموما غیر قابل شنیدن است ، زیرا فرکانس آنها با فرکانس مونتاژ چرخنده یکسان است.
- دما = افزایش دمای بیرینگ های در حال کار به دلیل افزایش دمای محیط رخ می دهد که بسته به نوع نصب متفاوت خواهد بود. هر گونه افزایش دمای فراتر از سطح طبیعی ، نشان دهنده شروع خرابی بیرینگ است.
- افزایش گشتاور چرخشی = حتی در هنگام نصب روی بیرینگ ها ، تمام سیستم های چرخشی یک گشتاور مقاومتی ایجاد می کنند. افزایش این گشتاور با افزایش احتمالی دما همراه است که نشان دهنده تغییر در عملکرد بیرینگ می باشد.
تفسیر نشانه های خارجی علت خرابی بیرینگ ها
لرزش
- لایه لایه شدن
- سطح ساییده شده ناشی از ذرات خارجی
- خوردگی ( زنگ زدگی )
- بارهای نامتوازن ناشی از سایش بیرینگ ها
- فاصله بیش از حد – به دلیل سفت بسته شدن حلقه
صدا
- فرورفتگی اجزای غلتک
- لایه لایه شدن
- درزگیری نادرست ( فرورفتگی ناشی از لرزش )
- ذرات خارجی
- خوردگی ( زنگ زدگی )
- از بین بردن فاصله داخلی ناشی از فشار وارده بیش از حد
- خرابی قفسه یا اجزای غلتک
افزایش دما
- روانکاری اضافی و یا عدم روانکاری
- حذف فاصله داخلی
- فشار بیش از حد ناشی از نصب نامناسب
- چرخش غیر طبیعی گشتاور
- کج شدن قفسه
- زوال روانکاری
- آسیب و یا جا به جایی آب بند
روش های کنترل پیشگیرانه
تناوب کنترل در اصل به قابلیت اطمینان قابل انتظار ، میزان استفاده از مواد و عوامل دیگری که مختص هر کاربر است ، بستگی دارد. کنترل های مبتنی بر طول عمر بیرینگ باید به صورت منظم انجام شود. کنترل خارجی بدین معناست که برخی ابزارهای کنترل که ارتعاشات غیرمعمول را تشخیص می دهند ، همچون ” متر صوتی ” ، در دسترس است. در هر صورت ، به منظور شناسایی واریانس باید به صورت تصادفی ” سطح مرجع ” را تعیین کنید.
شناسایی علت خرابی بیرینگ ها
تشخیص خرابی همیشه آسان نیست ، با این حال مراحل زیر می تواند مفید باشد :
- حقایق قابل توجهی در مورد بیرینگ و اجزای اطراف آن را ثبت کنید
- تمام دلایل احتمالی خرابی را شناسایی کنید
- از میان دلایل مشخص شده ، فقط دلایلی را انتخاب کنید که با حداکثر پارامترهای عملکرد غیر طبیعی مطابقت دارند
قبل از شروع روند حذف این علت خرابی بیرینگ ، با دقت هر یک از موارد زیر را بررسی کنید :
- وجود خاک
- افزایش دما به دلیل از بین رفتن روان کننده
- سطح صدا
- سطح گشتاور
- تکامل خرابی بیرینگ
- جهت بیرینگ در حین مونتاژ
بعد از حذف هر یک از موارد زیر را قبل از پاکسازی بیرینگ بررسی کنید ، در غیر اینصورت تجزیه و تحلیل شرایط دشوار می گردد :
- شرایط قفسه و اجزای غلتک
- شست و شوی بیرینگ
- بررسی روان کننده ، آب بند و حفاظ فلزی
- بررسی موقعیت بیرینگ و محل نصب حلقه
- بررسی محل قرارگیری شفت و نشیمنگاه
- بررسی سطح نصب ( به عنوان مثال شفت و نشیمنگاه )
- بررسی وجود خاک و خوردگی
انواع علت خرابی بیرینگ ها :
لایه ها ممکن است هم بر روی مسیر غلتش و هم بر روی اجزای غلتک وجود داشته باشند. آن ها ممکن است عمیق باشند ( تراشه های فرسوده ) و هم کم عمق! در هر دو مورد ، علل و علائم متفاوت است.
لایه های فرسوده
بیرینگ ها طول عمر محدودی دارند. بارهای عملیاتی که در آن ها به کار برده می شوند ، طول عمر فرسوده آن ها را مشخص می کند.
مکانیسم لایه های فرسوده
هنگامی که یک بیرینگ در معرض بار زیادی قرار می گیرد ، فشار در مسیر غلتش و اجزای غلتک ممکن است بسیار بالا باشد. حداکثر نیروهای برش در هزارم اینچ زیر سطح تماس ایجاد می شوند. این فشارهای تکراری از طریق حرکت مداوم اجزای غلتک ایجاد شده که نهایتا منجر به شروع روند لایه لایه شدن می گردد.
در نقطه ای با فشار بالا ممکن است شکاف های کوچکی در مواد ایجاد شود و به مرور این سطح ( شکاف ) افزایش یابد. به مرور زمان این ترک ها به هم می پیوندند و باعث می شوند فلزات در ناحیه ای که به سرعت در حال گسترش است پوسته پوسته شوند.
جوانب لایه ها
لایه لایه شدن یک پدیده تصادفی علت خرابی بیرینگ است که پس از پیدایش اولین ترک ، کم و بیش به سرعت پخش می شود. در نتیجه ، مواد لایه لایه شده باید در اولین مرحله تشخیص داده شوند زیرا به مرور زمان منجر به خراب شدن بیرینگ می گردند.
آغاز روند لایه لایه شدن
در مراحل اولیه ، سطح بیرینگ ممکن است برخی شکستگی های بدون اتصال را ایجاد کند.
منبع تصاویر و مطالب: وبسایت پلارد
مقاله چهارم: بررسی آماری خرابی بیرینگ ها
علت اصلی خرابی بیرینگ ها
نصب نامناسب (۱۶%):
نزدیک به ۱۶% از خرابی های زود هنگام برینگ ها به علت نصب اشتباه رخ می دهد و این در صورتی است که افراد متخصص و تعمیرکاران عموماً از وجود تجهیزات ویژه نصب بی اطلاع هستند. جهت نصب و راه اندازی و یا پیاده سازی درست برینگ ها روش های مختلف مکانیکی، هیدرولیکی و یا گرمایی وجود دارد که رعایت آنها از خرابی زود هنگام جلوگیری می کند.
روانکاری نادرست (۳۶%):
طبق تحقیقات انجام شده ۳۶% از خرابی های زودهنگام برینگ ها در اثر انتخاب نادرست و استفاده غیر حرفه ای از روان کننده ها رخ می دهد. به دلیل دسترسی سخت به محل قرارگیری برینگ در دستگاه ها، روان کاری دوره ای آن ها نادیده گرفته می شود که این امر می تواند آسیب های جدی ای به برینگ و دستگاه وارد نماید. یکی از راه های اطمینان از روان کاری مناسب برینگ ها، استفاده از سیستم های خودکار روان کاری می باشد.بیرینگ جهت کارکرد مطلوب باید بطور مناسب باید روانکاری شود تا از تماس مستقیم اجزاء با یکدیگر و سایش آنها و نیز جلو گیری شود.
در انتخاب گریس عوامل زیادی نظیر سرعت کارکرد و دما دخیل هستند و در این رابطه چندین نوع گریس مختلف موجود میباشد.روانکارها در اثر عواملی نظیر فرسودگی و ترکیب با مواد زائد، خواص روانکاری خود را از دست می دهند. لذا اضافه کردن گریس و تصفیه روغن در فواصل زمانی معین از مواردی است که باید حتما رعایت شود. در شرایط مختلف مانند: سرعت، فشار، دما ، از انواع مختلف گریس استفاده میشود.مزایای آن نسبت به روغن عبارت است از چسبندگی بهتر به برینگ و عدم چکه کردن به خصوص در مواقعی که شافت حالت عمودی داشته باشد و نیز عملکردی مشابه کاسه نمد در مقابل ورود بعضی مواد زائد و رطوبت به داخل بیرینگ.همچنین باید توجه داشت که گریس زیاد نیز موجب بالا رفتن سریع دما به خصوص در سرعتهای زیاد می شود، بنابراین فقط در مواقعی باید بیرینگ را کاملاً با گریس پر کرد که ۳۰ تا ۵۰ درصد فضای داخل محفظه با گریس پر شده و فضای آزاد کافی جهت انتقال گرما از بیرینگ به محیط اطراف از طریق گریس امکان پذیر باشد.
آلودگی (۱۴%):
از آنجایی که برینگ ها جزء تجهیزات دقیق محسوب می شوند، بدون رعایت عایق کاری صحیح قادر به کار در محیط های آلوده نمی باشند. عایق کاری صحیح باید هم برینگ و هم روان کننده آن را از هر نوع آلودگی حفظ کند. به طور کلی حداقل ۱۴% از خرابی های زود هنگام برینگ ها در اثر عایق بندی نادرست و ورود آلودگی به درون برینگ رخ می دهد.
خستگی (۳۴%):
وارد کردن فشار بیش از حد به دستگاه ها و یا سرویس نادرست آنها علت بیش از ۳۴% از خرابی های برینگ ها میباشد. این در صورتی است که با استفاده از دستگاه های نظارت بر عملکرد برینگ (Condition Monitoring Equipment) و هشدارهای آن ها می توان از این نوع خرابی ها جلوگیری نمود.
منبع تصاویر و مطالب : وبسایت آرسس صنعت
مقاله پنجم: دلایل خرابی بیرینگ ها و اقدامات رفع خرابی
یاتاقان (Bearing) قطعه ای است که ضمن کاهش اصطکاک، حرکت نسبی بین دو یا چند قطعه دیگر را ممکن می سازد و در انواع مختلفی وجود دارند. در این مقاله سعی کرده ایم علل خرابی یاتاقانها را بررسی و اقدامات لازم برای پیشگیری از خرابی و رفع عیوب احتمالی را بیان کنیم.

علل خرابی یاتاقان (Bearing) و اقدام متقابل
مقدمه
یاتاقان ها در اکثر ماشین ها از مهمترین قطعات هستند و یراساس ظرفیت و دوام آنها طبقه بندی می شوند.یاتاقان باعث کاهش اصطکاک چرخشی می شود و از بارهای شعاعی و محوری پشتیبانی می کند.
تعریف طول عمر یاتاقان
عمر مفید یاتاقان عبارت است از تعداد دورانی که یاتاقان می زند قبل از آنکه آثار خستگی ( ایجاد ترک ، پوسته شدن و …) در آن پدیدار شود. طول عمر یاتاقان معمولا برحسب ضریب میلیون دور یا بر حسب ساعتهای کارکرد آن و براساس قابلیت اطمینان ۹۰ درصدی تعریف می شود.
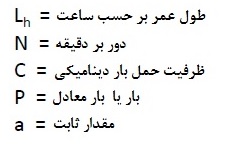
علل خرابی یاتاقان
بین طول عمر یاتاقان و سرویس نگهداری ماشین رابطه مستقیم وجود دارد. متاسفانه گاهی اوقات اتفاق می افتد که یاتاقان کمتر از طول عمر مورد انتظار و محاسبه شده، عمر می کند. دلایل زیادی برای این امر وجود دارد که شامل موارد زیر می باشد:
- بارگذاری بیش از حد
- روان کاری نامناسب و یا ناکافی
- حمل و نصب نامناسب
- آب بندی ناکارآمد یا جازدن بلبرینگ با زور و شفت سفت
- عدم وجود فضای کافی(بادخور)درون یاتاقان
چارت خرابی یاتاقان

انواع صدمات و خرابی یاتاقانها
آسیب اولیه
- فرسودگی
- تورفتگی
- لکه گیری(Smearing)
- تنش و آسیب سطحی
- خوردگی
- آسیب ناشی از جریان الکتریکی
آسیب ثانویه
- پوسته پوسته شدن
- ترک خوردن
- آسیب به محفظه
- آسیب ناشی از فرسودگی
آسیب فرسودگی

ممکن است این فرسودگی ناشی از ورود ذرات خارجی به درون یاتاقان یا روغنکاری نامناسب باشد. وجود لرزش در یاتاقانی که در حال چرخش نیست نیز میزان فرسودگی را افزایش می دهد.
سه نوع آسیب فرسودگی وجود دارد:
- فرسودگی ناشی از ذرات ساینده
- فرسودگی ناشی از روانکاری ناکافی
- فرسودگی ناشی از لرزش
فرسودگی ناشی از ذرات ساینده
علایم: دندانه های کوچک اطراف قسمت های غلتان و مسير گردش ساچمه هاى ياتاقان. سطوح فرسوده و مات .گریس تغییر رنگ داده شده.
علت: عدم پاکیزگی قبل ودرحین عملیات نصب. آب بندی نامناسب. روانکاری با روغن فرسوده
اقدام: کارگاه را تمیز نگه دارید و از ابزار تمیز استفاده کنید. آب بندی را چک کنید و تا حد ممکن آن را بهبود دهید. همیشه روان کننده تمیز و تازه استفاده کنید. روغن را از صافی عبور دهید.

فرسودگی ناشی از لرزش

لایم: ناصافی های مسیر گردش ساچمه ها. این ناصافی ها در یاتاقان های غلتکی بشکل مستطیلی و در یاتاقان های ساچمه ای به شکل دایره ای هستند. زیر این ناصافی ها ممکن است درخشان یا تیره و اکسید شده باشند.
علت: یاتاقان در حال سکون در معرض لرزش قرار دارد.
اقدام: یاتاقان را در حین حمل و نقل با پیش بارگذاری شعاعی محکم کنید. یک پایه محرک ارتعاشی را فراهم کنید. تا حد ممکن بجای یاتاقان غلتکی از یاتاقان ساچمه ای (بلبرینگ) استفاده کنید. تا حد ممکن از یک حمام روغن روانساز استفاده کنید.
تورفتگی
ممکن است بر اثر قرار دادن وزن دستگاه بر روی حلقه اشتباه و یا قرار داشتن در معرض بارگذاری غیرعادی درحالیکه در حال کار نیست، دچار تورفتگی در مسیر گردش ساچمه ها و اجزای غلتان گردد. همچنین وجود ذرات خارجی دریاتاقان باعث ایجاد تورفتگی می شوند.
دو نوع از آسیب های تورفتگی عبارت است از:
- تورفتگی ناشی از نصب نادرست یا اعمال بار اضافی
- تورفتگی ناشی از ذرت خارجی

تورفتگی ناشی از نصب نادرست یا اعمال بار اضافی
علایم: وجود تورفتگی در مسیر گردش ساچمه های هر دو حلقه با فاصله، معادل فاصله بین اجزای غلتان می باشد.
علت: در حین نصب فشار اشتباها به جای حلقه داخلی یاتاقان به محفظه گردگیر یا حلقه خارجی اعمال گردد. قرار گرفتن در معرض اضافه بار در حالیکه در حال کار نمی باشد.
اقدام: در حین نصب فشار را بر روی رینگ مناسب و مربوط قرار دهید. از اضافه بار اجتناب کنید یا از یاتاقان هایی که تحمل بار استاتیک پایه بالاتری دارند استفاده کنید.
آسیب ناشی از لکه گیری (Smearing)
وقتی دو سطحی که به مقدار کافی روانکاری نشده باشند تحت بار در خلاف جهت روی هم بلغزند، مواد از یک سطح به سطح دیگر منتقل می شود که به آن لکه گیری می گویند.

انواع آسیب های لکه گیری:
- لکه گیری انتهای غلتک وفلنج های راهنما
- لکه گیری غلتک و مسیر گردشه ساچمه ها
- لکه گیری مسیر ساچمه ها در فاصله ای مطابق با فضای غلتک ها
- لکه گیری سطوح خارجی
- لکه گیری یاتاقان کف گرد ساچمه ای
منحنی تغییرات سختی در مقابل زمان و دما
انجمن سازندگان یاتاقان در آمریکا، منحنی تغییرات سختی یاتاقان نسبت به زمان و دما را بصورت زیر بیان نموده است.

لکه گیری فلنج های راهنما و انتهای غلطک (Roller end)

علایم: خط افتادگی و تغییر رنگ انتهای غلتک و فلنج های راهنما
علت: قرار گرفتن تحت بار محوری سنگین بدون روان کاری مناسب
اقدام: روانکاری مناسب تر
لکه گیری مسیر گردش ساچمه ها

علایم: وجود رگه های لکه بصورت عرضی در فاصله ای معادل با فاصله بین غلتک ها، در مسیر گردش ساچمه های یاتاقان غلتکی استوانه ای
علت: لغزیدن غلتک بدلیل روانکاری بیش از حد
اقدام:
– بهبود پیش بار
– تمیزکاری بهتر یاتاقان
– استفاده از روان کننده مناسب با قابلیت ایجاد یک لایه خوب از فیلم روغن
– به کار گیری روش های روان کنندگی مناسب
– بهبود مکانیزمهای آب بندی
لکه گیری سطوح خارجی

علایم: خط افتادگی و تغییر رنگ سوراخ حلقه یا سطح خارجی یا ظاهر آن
علت: چرخش حلقه نسبت به شفت یا هوزینگ
اقدام: برای جلوگیری از چرخش شفت آن را چفت تر بگیرید و روشهای روانکاری را بهبود بخشید.
تنش و آسیب سطحی
اگرضخامت لایه روان کننده بین مسیر گردش ساچمه و اجزای غلتان خیلی نازک باشد، قسمت های بالایی سطوح ساچمه و کنس یاتاقان بطور لحظه ای با یکدیگر تماس برقرار می کنند . سپس ترک های کوچکی تحت عنوان تنش و آسیب سطحی در سطوح تشکیل می شوند. ترک های تنش و آسیب سطحی بسیار کوچک هستند ولی با گذشت زمان بتدریج چنان بزرگ می شوند بطوری که مانع از عملکرد نرم یاتاقان می شود.

علایم: در ابتدا آسیب بقدری کم است که با چشم غیرمسلح قابل رویت نیست. در یک مرحله پیشرفته تر، با ترک های کوچک و کم عمق همراه با سطوح شکاف دار کریستالی نمایان می شود.
علت: روانکاری ناکافی یا نا مناسب
اقدام: بهبود روانکاری
آسیب ناشی از خوردگی
خوردگی زمانی اتفاق می افتد که نفوذ آب یا مواد خورنده به درون یاتاقان به حدی باشد که روغن کاری، نتواند از سطوح فولادی حفاظت کند. طولی نخواهد کشید که این فرآیند موجب خوردگی عمقی می شود.

علایم: ظهور رگه های خاکستری- مشکی در سرتاسر مسیر عبور ساچمه ها، اغلب همزمان با گردش اجزای غلتان در آن. در مرحله بعدی،در این مسیر و دیگر سطوح یاتاقان، حفره هایی ایجاد می شوند.
علت:
– ورود گاز خورنده یا آب که مانع روغنکاری مناسب می شود
– تشکیل قطرات آب، ناشی از میعان رطوبت
– وجود دما و رطوبت بالا حین گردش
– عدم حفاظت مناسب در برابر خورندگی هنگام حمل و نقل
– شرایط نگهداری نامناسب
– به کار گیری و استفاده نادرست
اقدام:
– بهبود مکانیزم آب بندی
– بررسی روش های روان سازی
– انجام راهکارهای ضد خوردگی در طول غیر فعال بودن دستگاه
– بهبود روش های نگهداری
– بهبود روش های به کار گیری و استفاده
آسیب ناشی از جریان الکتریکی
وقتی یک جریان الکتریکی از یاتاقان عبور می کند، بطور مثال وقتی که از طریق اجزای غلتان از یک رینگ به رینگ دیگر انتقال می یابد، این آسیب رخ خواهد داد. درسطوح تماس،این فرآیند شبیه به جوشکاری قوس الکتریکی است.

علایم: ایجاد شیار(موج) به رنگ قهوه ای تیره یا خاکستری- مشکی و یا حفره هایی در مسیر عبور ساچمه ها و غلتک ها.ساچمه ها فقط تیره رنگ می شوند. گاهی اوقات سوختگی هایی بشکل زیگزاگ در مسیر عبور ساچمه های یاتاقان ها ایجاد می شوند.ظهور سوختگی های موضعی در مسیر عبور ساچمه ها و اجزای غلتان
علت: عبور جریان الکتریکی از یاتاقان در حال چرخش. عبور جریان الکتریکی از یاتاقانی که در حال چرخش نیست.
اقدام: طراحی مدارهای الکتریکی (مسیر عبور جریان) به گونه ای که از عبور جریان از یاتاقان ها جلوگیری شود. عایق کاری یاتاقان .
پوسته شدن
فرسودگی، نتیجه تنش سطحی گردشی است که به سرعت در قسمت زیرین سطح حمل کننده بار ظاهر می شود. بعد از گذشت مدت زمانی، این تنش ها باعث ایجاد ترک هایی می شوند که بتدریج به کل سطح گسترش می یابند. هنگامی که اجزای غلتان به این ترک ها می رسند باعث جدا شدن ذراتی از آن می شوند که این فرایند به پوسته شدن(Flaking) معروف است.

علایم:خیلی واضح بودن الگوی حرکت در مسیر عبور ساچمه ها در هر دو رینگ، پوسته شدن معمولادرناحیهای که بیشترین بارگذاری در آن ناحیه انجام شده است اتفاق می افتد و بافت زبر و خشن.
علت:
– اضافه بار
– نصب نامناسب(نامیزان)، ورود ذرات خارجی، روانکاری ضعیف، روان کننده نامناسب، عدم در نظرگرفتن بادخور مناسب برای یاتاقان
– عدم دقت کافی در نصب شفت یا محفظه
– پیشرفت خوردگی، حفره های خوردگی، لکه دار شدن، تورفتگی
اقدام:
– روش نصب و مکانیزم آب بندی را بهبود ببخشید. یک روان کننده با ویسکوزیتی مناسب استفاده کنید.
– روش روانکاری را بهبود ببخشید،دقت نشیمنگاه بلبرینگ بر روی شفت و هوزینگ را بررسی کنید.
– فضای آزاد(بادخور) داخلی یاتاقان را چک کنید.
آسیب ترک دار شدن
ترک های ظاهر شده در یاتاقان در اثر عوامل بسیاری ایجاد می شوند. رایج ترین علت، برخورد با جسم سخت هنگام نصب یا باز کردن آن است. ضربه زدن، انجام اعمالی بر روی رینگ که منجر به شکستگی بخشهای از یاتاقان می شود.

ممکن است ترک ها به دلایل زیر ایجاد شوند :
– برخورد با جسم سخت یا زبر
– سایش
– لکه دار شدن
– راه اندازی در شرایط اضافه بار
علایم: ترک ها یا قطعه های شکسته شده، عموما در یک سمت یاتاقان
علت:
– تداخل بیش از حد
– اضافه بار ، بار ضربه ای
– پیشروی پوسته شدن
– تولید گرما و اصطکاک بدلیل ایجاد تماس بین قطعات نصب شده با رینگ ساچمه دار
– ایجاد گرمای ناشی از خزش
– زاویه شیب نامناسب در شفتهای مخروطی
– استوانه ای بودن ناکافی شفت
اقدام:
– تداخل اضافی را تصحیح کنید.
– شرایط بار را چک کنید.
– روش نصب را بهبود بخشید.
– از یک شفت با شکل مناسب استفاده کنید.
آسیب قفسه نگهدارنده ساچمه ها

دلایل روشنی برای آسیب به قفسه نگهدارنده ساچمه ها وجود دارد : ارتعاش – سرعت بیش از اندازه – فرسودگی – انسداد – شکستگی قفسه
علایم: ترک ها، تغییر شکل قفسه نگهدارنده ساچمه ها، شکستگی
علت:
– نصب نادرست (عدم همترازی یاتاقان)
– استفاده نادرست
– اعمال شوک و لرزش شدید
– سرعت گردش بیش از اندازه ، افزایش و کاهش سرعت های ناگهانی
– روانکاری ضعیف
– افزایش دما
اقدام:
– روش نصب را چک کنید.
– دما، چرخش و شرایط بار را چک کنید.
– لرزش را کاهش دهید و از پایه کاهنده لرزش استفاده کنید.
– نوع قفسه نگهدارنده ساچمه ها را به درستی انتخاب کنید.
– از یک روش روان سازی و یک روان کننده استفاده کنید.
سلام، این یک دیدگاه است.
برای شروع مدیریت، ویرایش و پاک کردن دیدگاهها، لطفا بخش دیدگاهها در پیشخوان را ببینید.
تصاویر نویسندگان دیدگاه از Gravatar گرفته میشود.